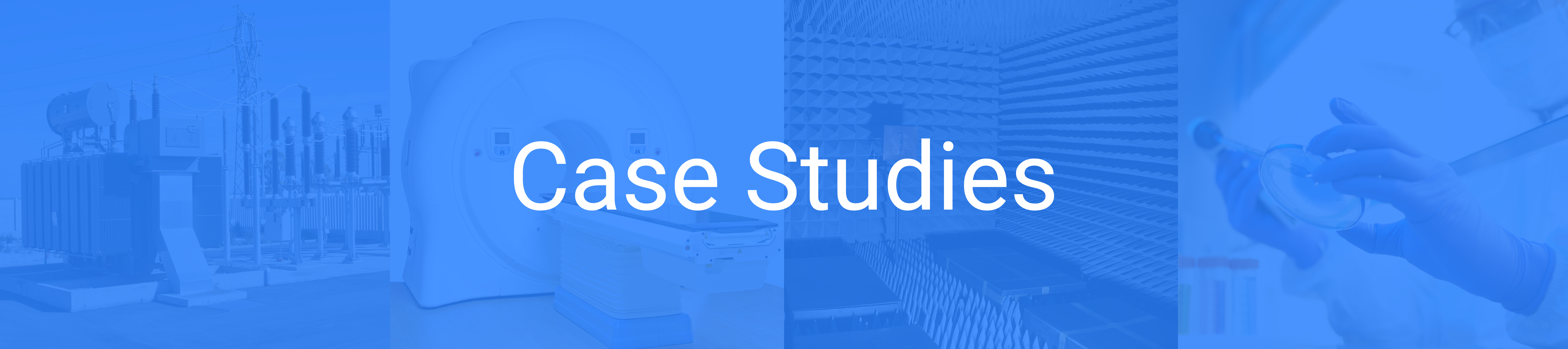
POLYMER ROBOTICS
Fiber Optic Linear Encoders Guide MRI-Guided Biopsy Robot
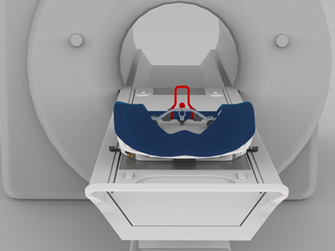
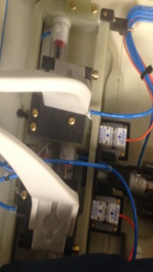
Application:
Prostate cancer is the second most cancer related cause of death in men. PSA blood screening and Digital Rectal exams are the typical method for initially detecting possible presence of prostate cancer. A positive exam result would then lead to a biopsy and/or MRI imaging for verification. The increasing cost of cancer treatment has opened up creative opportunities for reliable methods for early detection.
Current prostate biopsy such as transrectal ultrasound guidance (TRUS) use sound waves to make an image of the prostrate. However, TRUS can’t tell the difference between normal tissue and cancer so the doctor guides himself to the prostrate, inserts a need through the wall of the rectum, and takes a biopsy sample. He repeats this process several times to assure that every area of the prostate has been sampled but areas can be missed. Also TRUS biopsy has a small but significant risk of serious infection since the rectal wall cannot be sterilized.
MR Guided Biopsy allows for very precise manual placement of the biopsy needle under a direct guidance of MRI. Polymer Robotics has taken the approach to automate the prostrate biopsy process by developing a transperineal MRI-guided Biopsy Robot, combining the low risk of infection by entering through the perineum (body between scrotum and anus) and the high resolution and accuracy of real-time MRI guidance.
The Polymer Robotics Falcon™ is the world’s first transperineal MRI-guide targeting system for prostate cancer. The Falcon requires 5 degrees of freedom (DOF) which requires high precision, non-metallic feedback sensors that can operate within the extreme magnetic field environment of an MRI bore.
Requirements:
Summary of requirements:
- Up to 16 inches of linear travel
- 0.1mm resolution
- Non-metallic
- Durability and repeatability over 200,000 cycles
- Absolute position after start-up
- Withstand MRI-generated as well as sound-induced vibration
Solution:
When approached by Polymer Robotics in early 2014, Micronor proposed to utilize an incremental, linear sensor concept which was currently in development for a welding robot. Based on the proven and patented 2-phase/2-wavelength optical encoder system, a new miniature “read head” was designed. This read head consists of a ceramic subcarrier for the high precision optical components and the film guide molded from Acetal plastic material. This new optical read head is small enough to fit into very tight areas.
The success of the prototype led to the final design of the MR303 MRI Safe Linear Encoder and the MR302-2 OEM Controller. For 5 axis DOF, the customer required 4 sets of sensors and controllers for Falcon™ proof-of-concept. The first set was delivered in May 2014 with machined plastic bodies. Mold tools were subsequently completed and first production parts were later run without problems. Additional Falcon™ systems have been assembled for Phase II and subsequent human testing.
Environmental testing of the linear encoder followed and met all requirements. An active durability test of the sensor/film strip combination showed no performance degradation at initial test run of 250,000 cycles. Subsequent testing has verified operational durability beyond 500,000 cycles under simulated MRI-induced sound vibration.
The MR303, the world’s first MRI safe fiber optic linear encoder, was commercially released in June 2015.
Implementation:
Because of the proprietary nature of medical devices, internal details of the Falcon™ robot are not available but the MR303 position feedback has met expectations. An internal photograph shows two of the MR303 sensors and portions of the MRI compatible pneumatic drive system.
Products Used (per system):
- MR303-B400C1R5 MRI Safe Linear Encoder (current product is MR343-B400C1R5), Qty 4
- MR302-0 OEM Controller (current product is MR340-0), Qty 4
- EC-TD5334-XXX series Encoder Film Strips, Qty 4