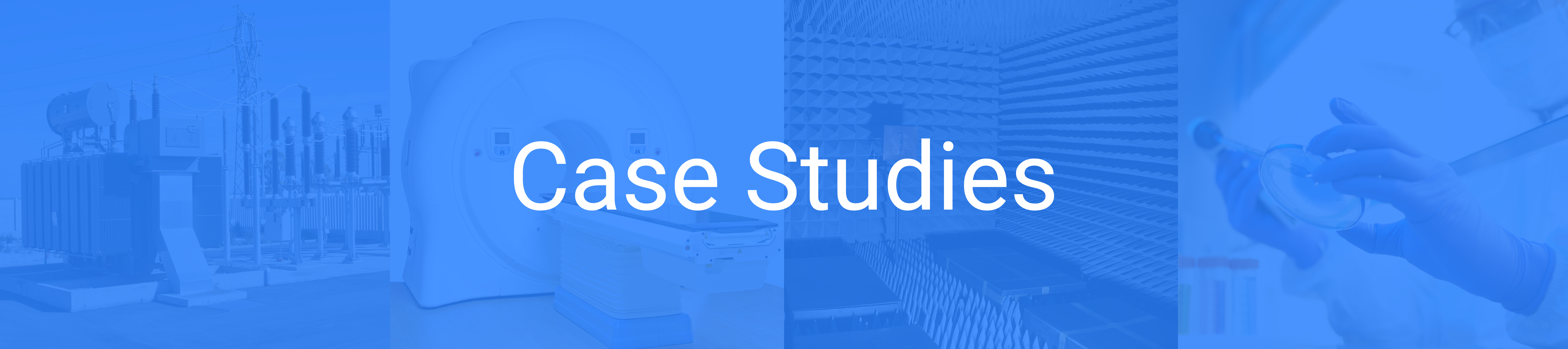
Electric Arc Furnace
Monitoring Electrode Position in an EAF
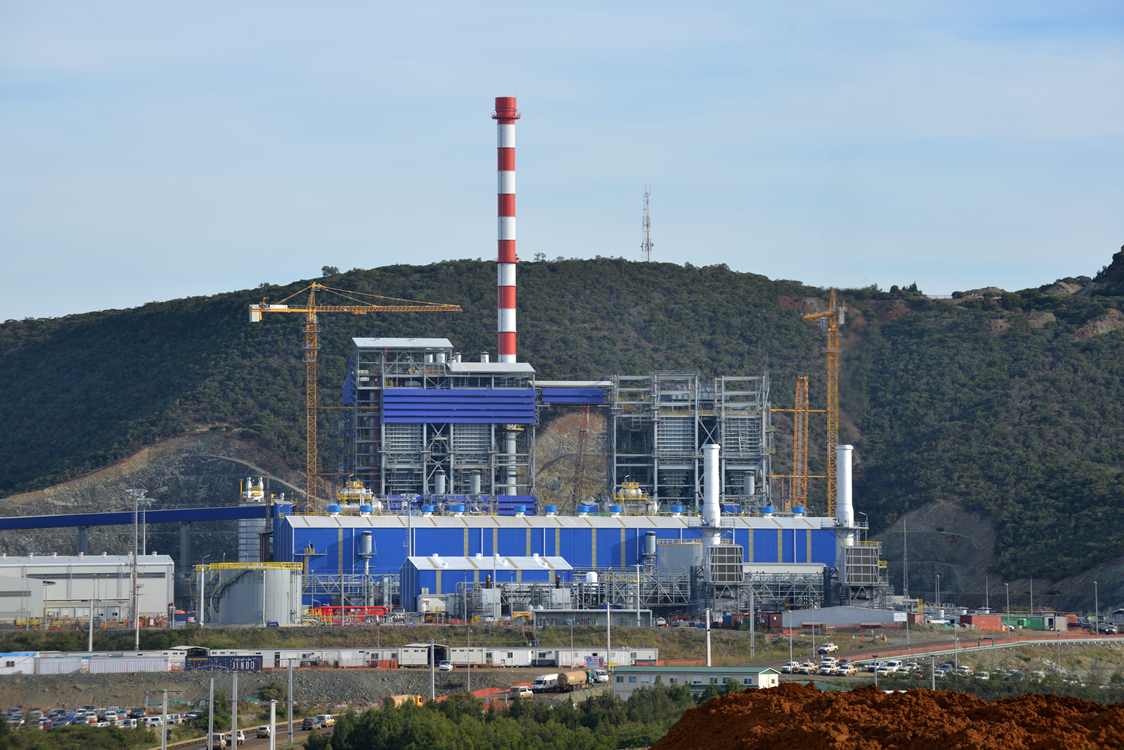
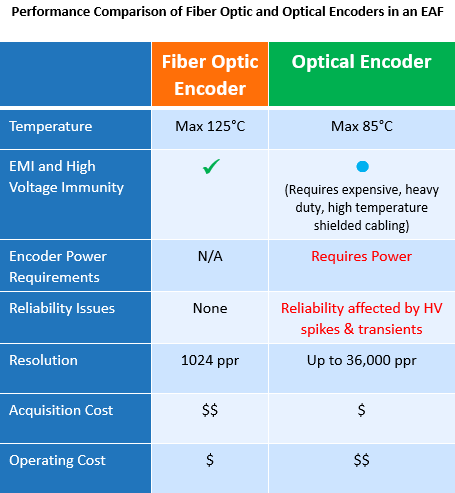
Application Description:
The Koniambo mine is one of the largest nickel reserves in New Caledonia, with over 150 million tonnes of nickel metal. Nickel is taken from the Koniambo Massif to a smelter on the coast of the island via a conveyer. Throughout the nickel smelting process, temperatures can reach up to 1350°C in order to purify the nickel ore into pure nickel.
A typical electric arc furnace (EAF) heats charged material by means of an electric arc. It is a common method for processing raw and scrap steel, platinum, silica and other ores. Mid-size furnaces operate at 60,000,000 Volt-Amperes (60 MVA) with a secondary voltage of 400-900 V at up to 44,000 A.
Requirements:
A servo motor or hydraulic cylinder controls electrode position, making position feedback and control critical to performance. Within the EAF, the carbon/graphite electrodes wear over time, and electrode position must be monitored for optimal ore processing. The equipment operates at sustained elevated temperature and within a high electrical noise environment.
Solution:
The size and parameters of the specific furnace define the operating environment for the position sensor. While the typical solution is an incremental encoder, fiber optic encoders have also been used.
Fiber optic encoders, such as Micronor’s MR344 hollow-shaft incremental encoder, are best suited for harsh environments where EMI and high voltage immunity are required. The MR324 also does not require power to run and has no reliability issues, lowering operating costs in the long-term.
Meanwhile, traditional optical encoders provide a lower cost of acquisition and higher achievable resolution (up to 36,000 ppr vs. the MR344’s 1024 ppr). These encoders also require power to run and their reliability can be affected by HV spikes and transients, leading to greater long-term operating costs.
Implementation:
The photo shows an MR344 hollow-shaft incremental encoder driven by a friction wheel contacting the electrode surface. As the electrode moves up or down, the encoder provides optical signals to the remote MR340 controller module allowing for precise position feedback.
Products Used:
- MR344 High Resolution Hollow-Shaft Incremental Encoder, Qty 1
- MR340-1 DIN Rail Mount Controller, Qty 1