What type of encoder does your application require?
- Absolute encoders (also called position sensors) are used where monitoring absolute position and high precision are required. There are two types: single turn (output over one revolution, 0-360 degrees) and multiturn (provides single turn position and track # of turns up to 65,536 revolutions. Their signature output is a digital value of absolute position via any number of interface options – SSI, Analog, Profibus, CANopen, Ethernet, etc. SSI (synchronous serial interface) is considered the native, most robust absolute encoder interface option. Even if an absolute encoder loses power, an absolute encoder will always report it current true position upon start-up. Micronor Sensors also offers conventional Electromechanical (electronics-based, typically optical or magnetic) and Fiber Optic Absolute Encoders (where immunity to interference, emi/rfi, rf, microwaves, magnetic fields, electrical fields, radiation, or long distance operation is required).
- Incremental encoders are used where speed and relative position need to be monitored, and typically offer lesser resolution than an absolute encoder system. Their signature outputs are A/B quadrature pulses. The user’s motion control system tracks these pulses (phasing determines direction) to monitor relative position from initial Home setting. The same system measures the time between pulses to track speed. If the system loses power, all position and speed information is typically lost. Micronor Sensors also offers conventional Electromechanical (electronics-based, typically optical or magnetic) and Fiber Optic Incremental Encoders (where immunity to interference, emi/rfi, rf, microwaves, magnetic fields, electrical fields, radiation, or long distance operation is required).
- Fiber Optic Encoder Extenders can extend the operating distance of conventional Electromechanical encoders (absolute or incremental, but choose the right matching one).
Absolute Encoders
Shafted and Hollow Shaft Encoders with Analog Output or SSI interface for Absolute Position Feedback
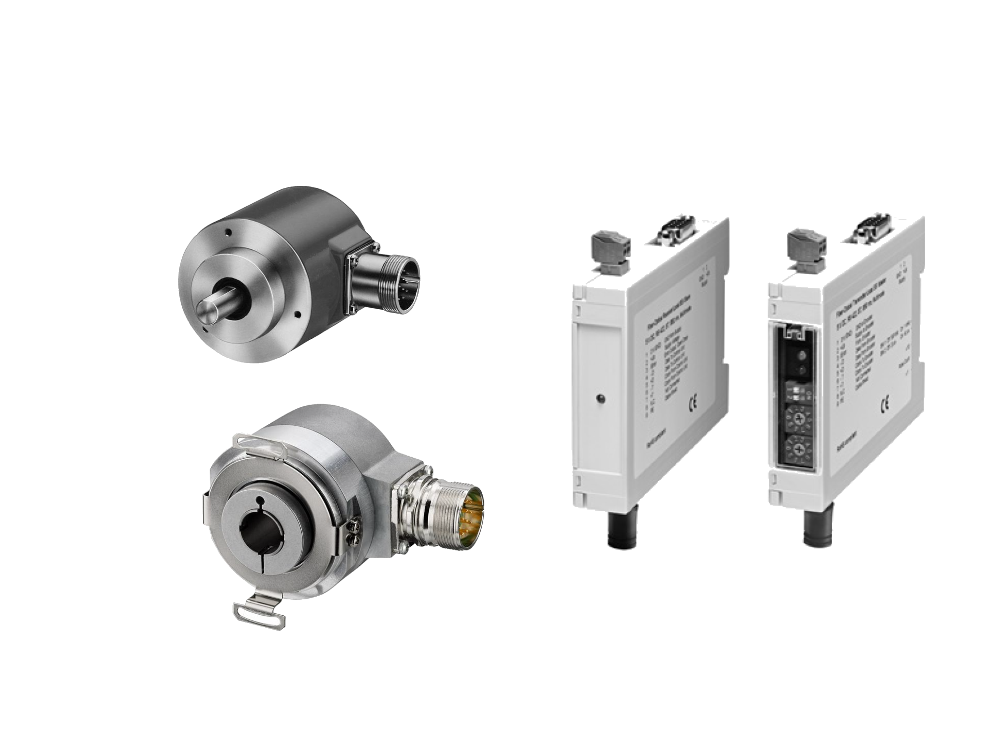
High performance, highly reliable absolute encoders, both shaft and hollow shaft configurations.
Need to extend the reach of an existing SSI Absolute encoder up to 2000m – check out our MR361-2 series Fiber Optic Encoder Extender Systems
For use with SSI Absolute Encoders, check out the MR361-2 series fiber optic extender system.
Looking for Absolute Encoder with 4-20mA or 0-10V analog output?
We offer two models, single turn ESAV361/ENAV361 series and multiturn ESAV36/ENAV36 series. Both models are programmable with the single turn having a SET input for setting the 4mA position while the multitum models has SET1 (4mA) and SET2 (20mA) inputs..
Looking for Absolute Encoder with SSI output?
We offer the universal, ruggedized multiturn shafted ESAMX58 series and hollow shaft ENAMX58 series, both with SSI (synchronous serial interface) and BISS (bi-directional serial synchronous interface) options.
Looking for Draw Wire Absolute Encoder System with Analog output or SSI interface?
Consult the product page Draw Wire Linear Limit Switches and Encoders for guidance. Next, identify identify the following parameters and then contact Micronor Sensors sales:
- Full length of travel? Determines draw wire module size/length.
- Linear resolution required? Determines encoder resolution. Typical travel is 300mm/encoder input revolution.
- Interface requirement – 4-20mA, 0-10V or SSI
- Display readout required? Display units desired (ft, m, mm, etc.)Units desired?
Looking for Measuring Wheel Encoder System for tracking absolute position with Analog or SSI output?
Consult the product page Measuring Wheel Encoder Systems for guidance. Next, identify the following parameters and then contact Micronor Sensors sales:
- Type of media to track? Typical applications: EAF electrode, paper, plastic, metal, cloth, etc.
- Length of travel? Standard wheels have circumference of 500mm., option 200mm wheel.
- Linear travel resolution per pulse required?
- Type of interface: 4-20mA, 0-10V or SSI?
- Display readout required? Units desired?
Incremental Encoders
Shafted and Hollow Shaft Encoders with Quadrature Pulse Outputs for Speed and Relative Position Feedback
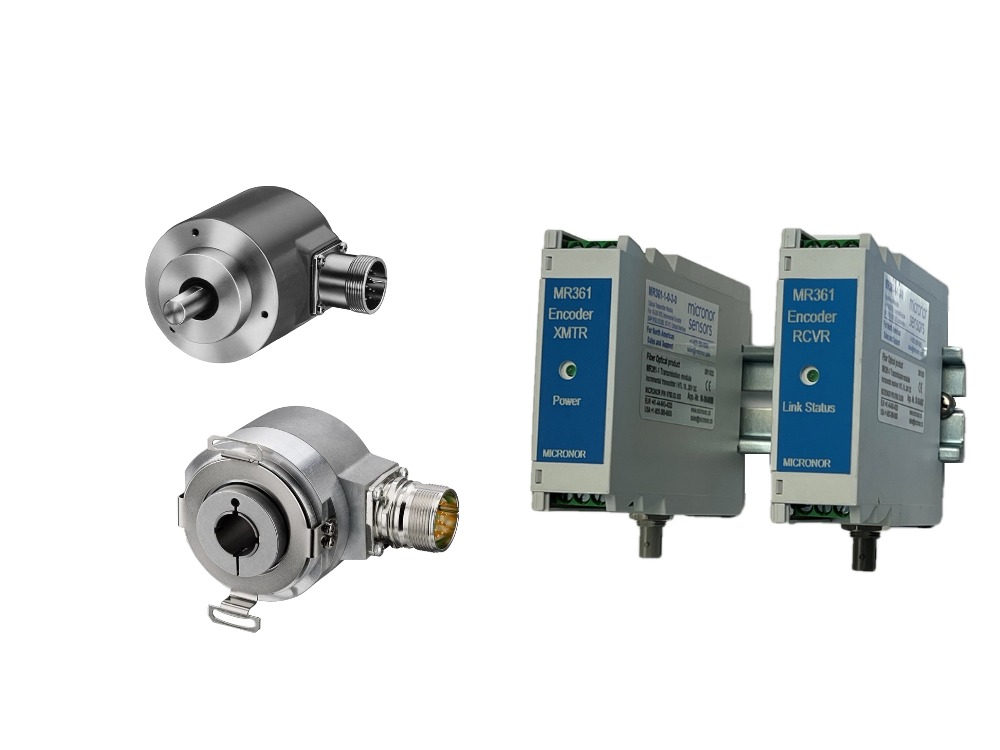
High performance, highly reliable incremental encoders, both shaft and hollow shaft configurations.
Need to extend the reach of an existing encoder up to 2000m – check out our MR361 series Fiber Optic Encoder Extender Systems
For use with Incremental Encoders, check out the MR361-1 series fiber optic extender system.
Looking for Incremental Encoder with A/B/Z quadrature outputs?
For standard applications (1-3’6000 ppr), check out the shafted ESIX50 series and hollow shaft ENIX50 series.
For high temperature applications (-20C to +105C, 10-5000 ppr), check out the shafted ESI58T series and hollow shaft ENI58T series.
For high resolution applications (7’200 to 36’000 ppr), check out the shafted ESI58HA series and hollow shaft ENI58HA series. Many of our meltshop customers use the high resolution 36’000ppr ESI58HA.1265.36000 encoder as part of our MRAD series measuring wheel system for monitoring EAF Anode Position/Slippage.
For high temperature applications (-20C to +105C, 10-5000 ppr), check out the shafted ESI58T series and hollow shaft ENI58T series.
Looking for Draw Wire Incremental Encoder System with A/B/Z quadrature outputs?
Consult the product page Draw Wire Linear Limit Switches and Encoders for guidance. Next, identify identify the following parameters and then contact Micronor Sensors sales:
- Length of travel? Determines size/length of draw wire module
- Resolution per pulse required? Typical internal draw wire travel is 300mm/encoder input revolution.
- Display readout required? Position or speed? What display units are required?
Looking for Measuring Wheel Incremental Encoder System with A/B/Z quadrature outputs?
Consult the product page Measuring Wheel Encoder Systems for guidance. Next, identify the following parameters and then contact Micronor Sensors sales:
- Type of media to track (EAF electrode, paper, plastic, metal, cloth, etc.)
- Length of travel? Standard wheels have circumference of 500mm, optional 200mm wheel.
- Linear travel resolution per pulse. Determine resolution of incremental encoder.
- Display readout required? Position or speed? What display units are required?